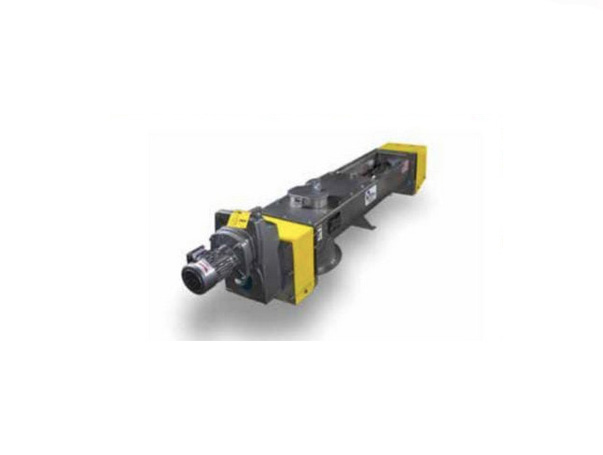
Screw feeders are designed to meter bulk materials and are usually located at the beginning of a process. With screw feeders, capacity or feed rate can be precisely controlled. With variable speed drives, metering is more accurate, and feed rates can be varied.
In a simple type of screw feeder, rotation of the screw moves a continuous plug of material into the pipeline, where it is dispersed and entrained with the conveying air. Screw feeders are particularly advantageous because screw speed and material feed rate are approximately linearly related, which allows discharge rate control within narrow limits.
The feed rate is unlikely to be affected by screw feeders and rotary valves because they are positive displacement devices. As a result, a reduction in conveying-line pressure drop will be regarded as an improvement in performance, it would be recommended that the screw valve or rotary valve be cranked faster to increase material flow.
The Design Parameters of Screw-Feeder:
- Product Type: Wood Chips and Saw Dust
- Material Density: 10 to 15 Lbs. per Cubic Foot
- Design Temperature: 1,400-Degrees F
- Conveyor System Capacity: 2,700 Cubic Feet per Hour
- Duty: 24 hours per Day, 7 Days per Week
The new screw feeder was made of 316 stainless steel to withstand the high heat coming from the furnace. The screw feeder housing was made from 20-inch schedule 40 pipe to provide a rigid housing for the screw. Screw diameter was selected to account for thermal expansion and avoid interference between the screw and housing. It provided a double bearing arrangement on the drive end to support the screw and allow thermal expansion into the furnace. A shaft-mounted reducer with torque arm bracket eliminated any potential alignment issues. The tail end of the screw was located inside the furnace and subjected to 1,400-degrees F. It has been designed and manufactured by a special tail end bearing made from Hastelloy to handle the high temperature. Ceramic flange gaskets and seal rope packing kept the screw feeder airtight. Shaft guards on the drive end were supplied to protect operators.